A REVOLUTION IN CORROSION PREVENTION
From Decay to Durability: Coatings that Redefine Corrosion Prevention
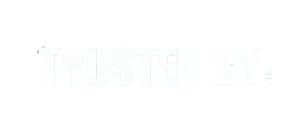
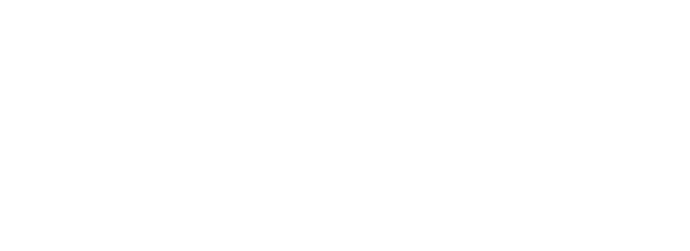
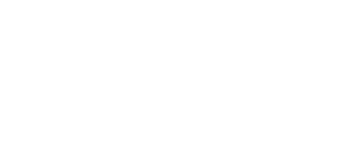
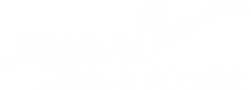
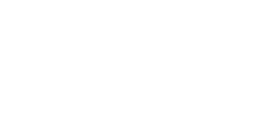
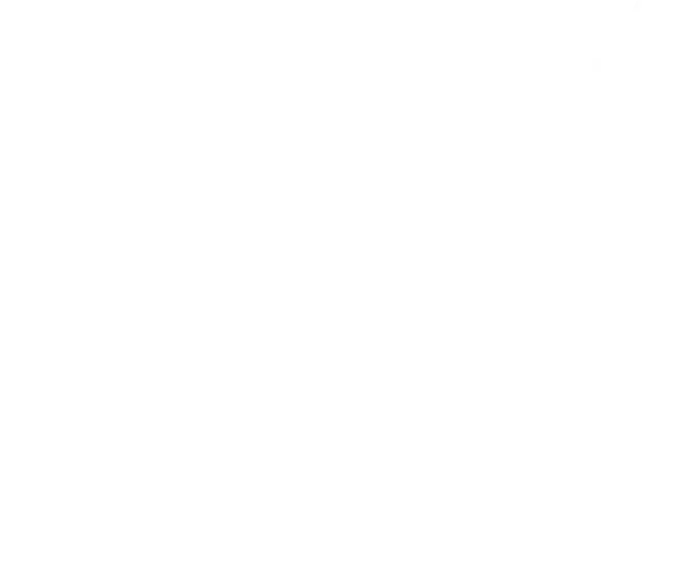
MEET METGUARD
A CONCEPTUAL ADVANCE IN METAL PROTECTION
Metguard is a unique metal passivating protective coating, arresting corrosion of metals at its core. Challenging conventional norms, Metguard offers a cost effective, greener & technologically advanced solution to corrosion prevention.
- FIRST TIME IN THE WORLD
- PATENTED
- COPYRIGHTED
UNIQUE METAL PASSIVATION TECHNOLOGY
Metguard works on the principle of metal passivation. Unlike conventional protective coatings such as expoxies, alkyds, polyurethanes (PU), etc that offer mere barrier protection, Metguard possesses the remarkable capability to passivate active metals, suppressing their reactivity with the environment to arrest corrosion at its core.
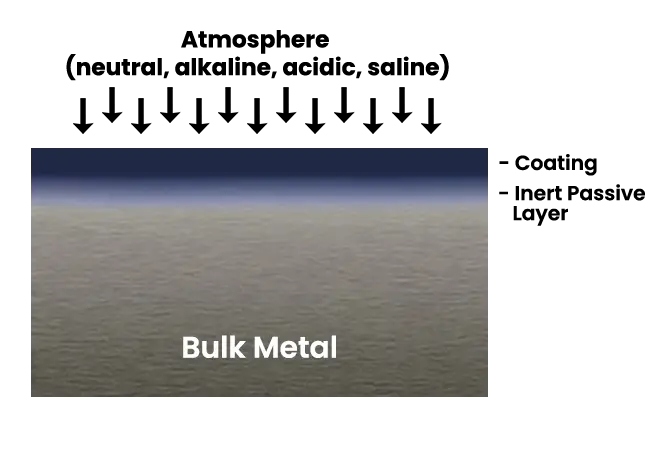
NEW HORIZONS
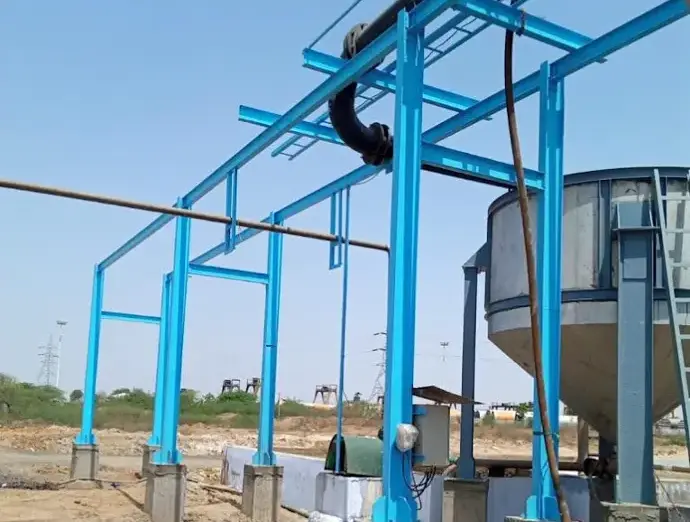
EXPONENTIALLY INCREASES METAL LIFE
Metguard exponentially increases metal life by virtually eliminating active metal loss through in situ passivation at the coating-metal interface, reducing metal scrappage and replacement.

ELIMINATES ABRASIVE BLASTING
Metguard can be applied directly on rusted surfaces as well as new structures (including mill scale covered HRS) without any complex surface preparation—only loose rust needs removal.
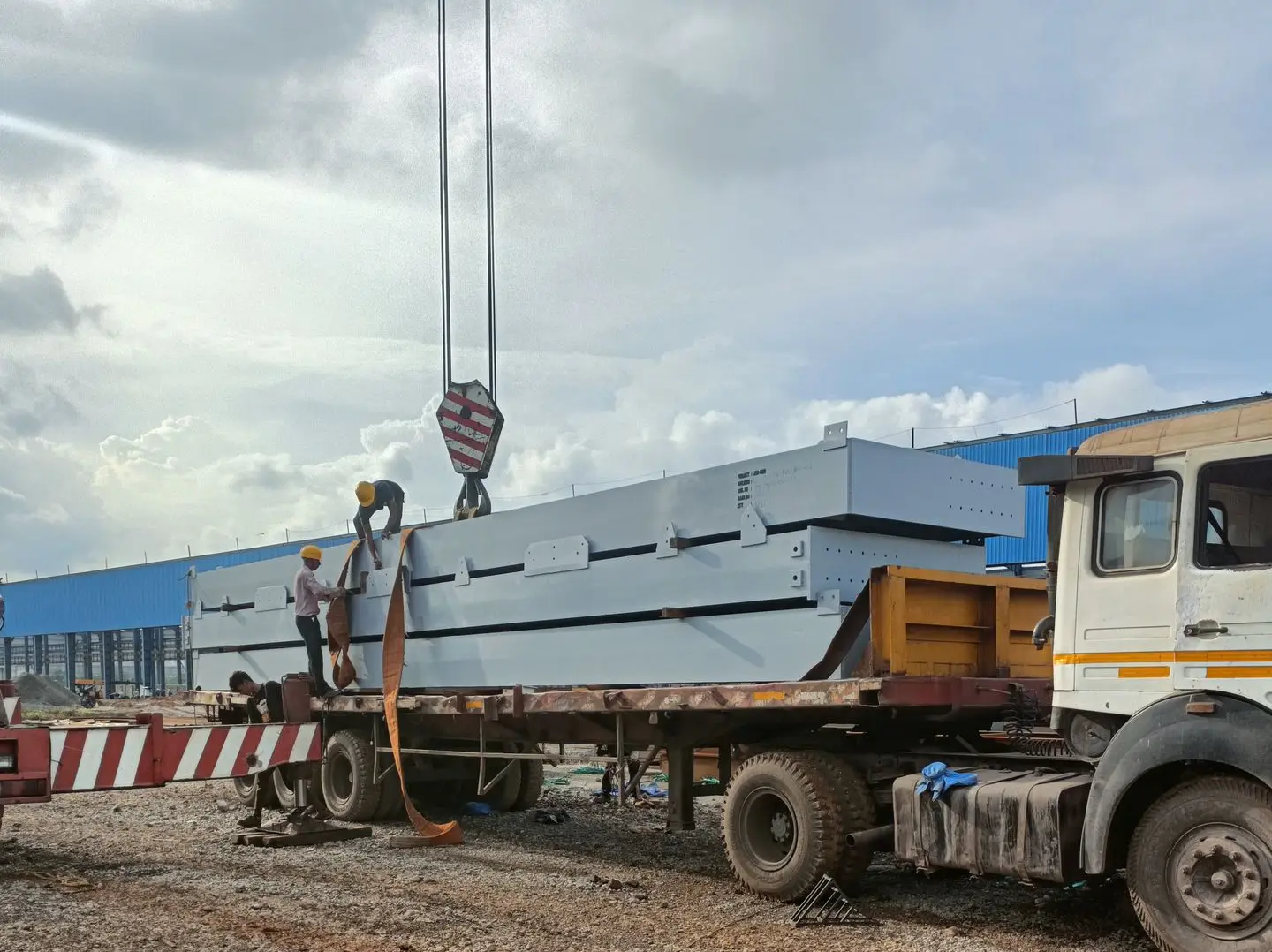
EASES MAINTENANCE, REDUCES DOWNTIME
Metguard reduces plant downtime and lifecycle costs through its easy maintenance- simply reapply the top coat at specified intervals without stripping the existing coating.
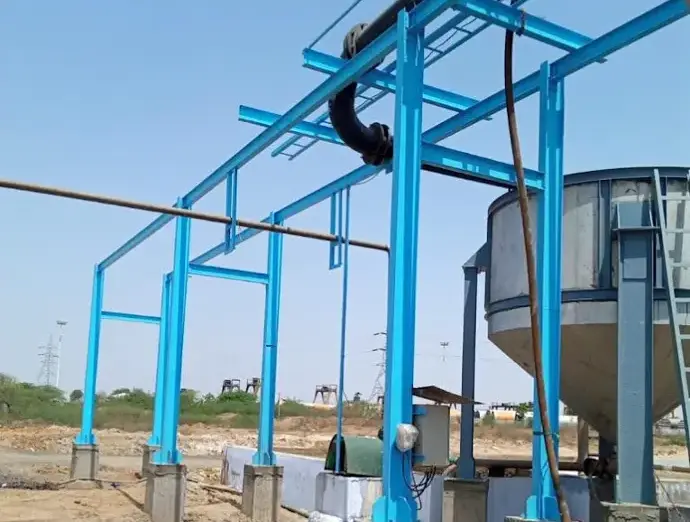
EXPONENTIALLY INCREASES METAL LIFE
Metguard exponentially increases metal life by virtually eliminating active metal loss through in situ passivation at the coating-metal interface, reducing metal scrappage and replacement.

ELIMINATES ABRASIVE BLASTING
Metguard can be applied directly on rusted surfaces as well as new structures (including mill scale covered HRS) without any complex surface preparation—only loose rust needs removal.
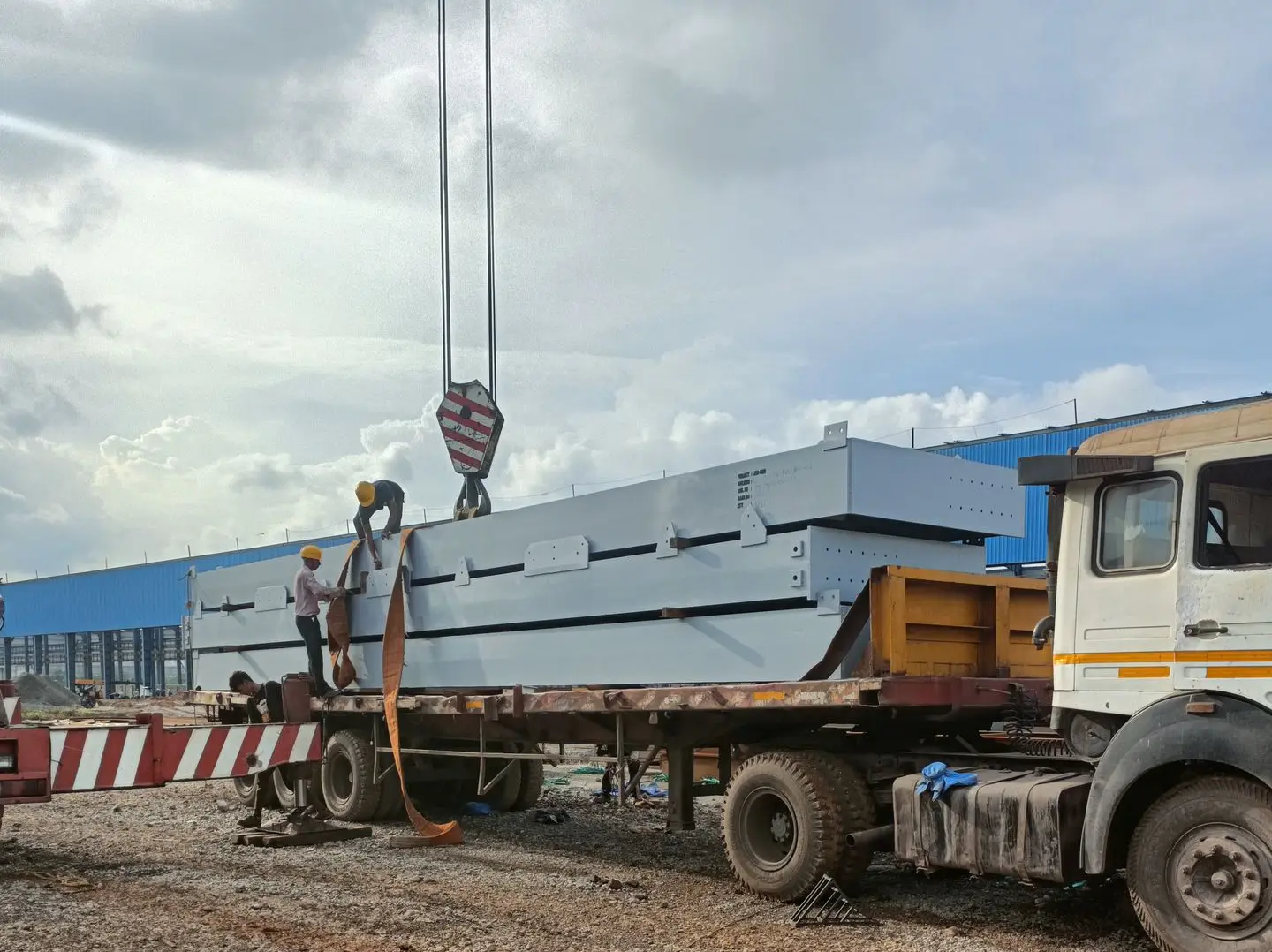
EASES MAINTENANCE, REDUCES DOWNTIME
Metguard reduces plant downtime and lifecycle costs through its easy maintenance- simply reapply the top coat at specified intervals without stripping the existing coating.
ENHANCES LIFE OF METALLIZED STEEL
Metguard duplex coatings, on HDG, other metallized steel, & aluminium alloys, arrest depletion of reactive metal, thereby extending galvanic protection of steel.
THIN-FILM PROTECTION
Metguard provides superior protection to all metals in lower DFT than barrier coatings.
ECO-FRIENDLY TECHNOLOGY
Free from chromates, isocyanates, halogens, and lead, Metguard is an environmentally friendly solution for sustainable corrosion protection.
ENHANCES LIFE OF METALLIZED STEEL
Metguard duplex coatings, on HDG, other metallized steel, & aluminium alloys, arrest depletion of reactive metal, thereby extending galvanic protection of steel
LONG POT LIFE
Metguard offers a long pot life, making it ideal for application on both new and existing structures, ensuring convenience and efficiency.
ECO-FRIENDLY TECHNOLOGY
Free from chromates, isocyanates, halogens, and lead, Metguard is an environmentally friendly solution for sustainable corrosion protection.
POTENTIAL APPLICATIONS
- Replacement of hot dip galvanized steel structures especially in acidic / alkaline areas
- Reduction of material & energy costs in cathodic protection through thin film coatings on steel
POTENTIAL APPLICATIONS
- Replacement of hot dip galvanized steel structures especially in acidic / alkaline areas
- Reduction of material & energy costs in cathodic protection through thin film coatings on steel
UNMATCHED PERFORMANCE
ELECTROCHEMICAL IMPEDANCE STUDIES
Maintains Rp at Giga ohm.cm on coated non-blasted HRS (Hot Rolled Steel) & rusted steel, for more than 4000 hours of constant exposure.
SALT SPRAY TEST
Passes 2000 hours with zero creep from scribe, on coated non-blasted HRS & non-pretreated HDG (Hot Dip Galvanized steel), under constant salt fog exposure.
ADHESION
Exceptional adhesion to existing corroded and new substrates (including mill scale covered HRS): 200 microns DFT passes 5B (1mm grid).
TOUGHNESS & COHESIVE STRENGTH
Scratch/gouge hardness of 5 Kg (in composite DFT of 200 microns) with excellent flexibility.
HEAT RESISTANCE
Outstanding resistance to dry heat (up to 200°C) and thermal cycling.
UNRESTRICTED APPLICATION
Protects in acidic/ alkaline, saline, humid, and strong UV exposures - C3 up to CX environments.
WHERE THERE IS METAL, THERE IS METGUARD
CAN BE APPLIED ON:
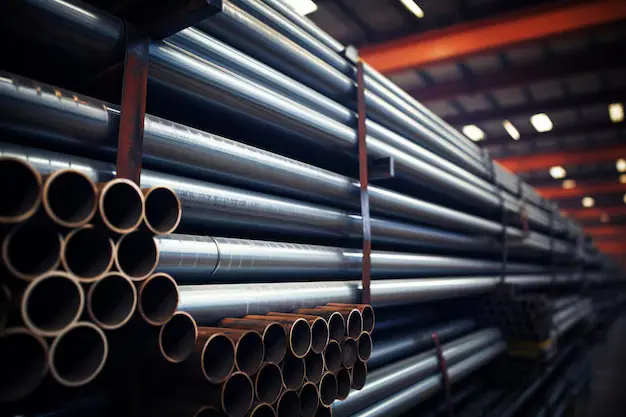
All new steel structures in stockyards and fabrication centers (including tubular structures like pipes)

All existing corroded steel structures
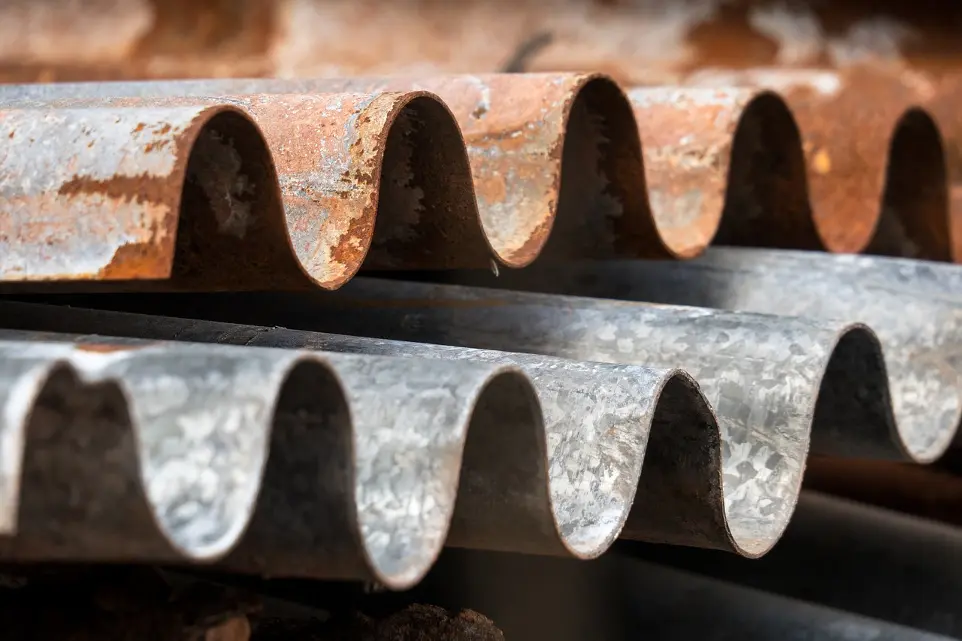
Galvanized/ Zinc-aluminium Sheets & Structures (New & existing corroded)
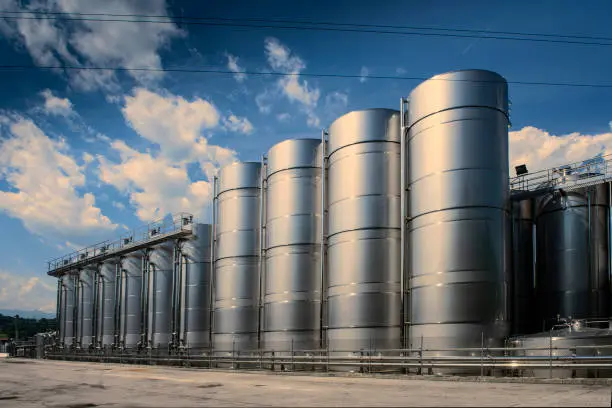
Stainless & other ferrous alloy structures (New & existing corroded)
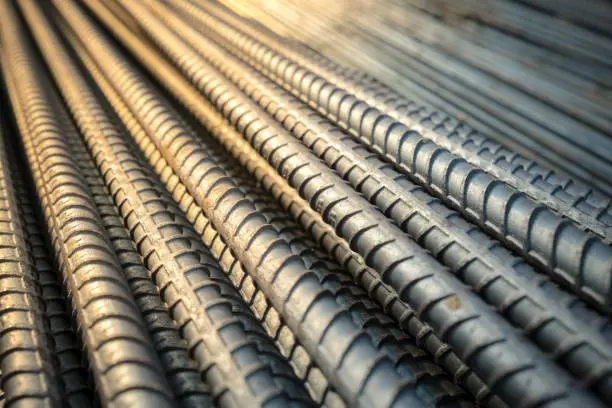
Concrete embedded steel structures: re-bars, etc
IN VARIOUS INDUSTRIES SUCH AS:
...AND MANY MORE
LOWEST LIFECYCLE COST
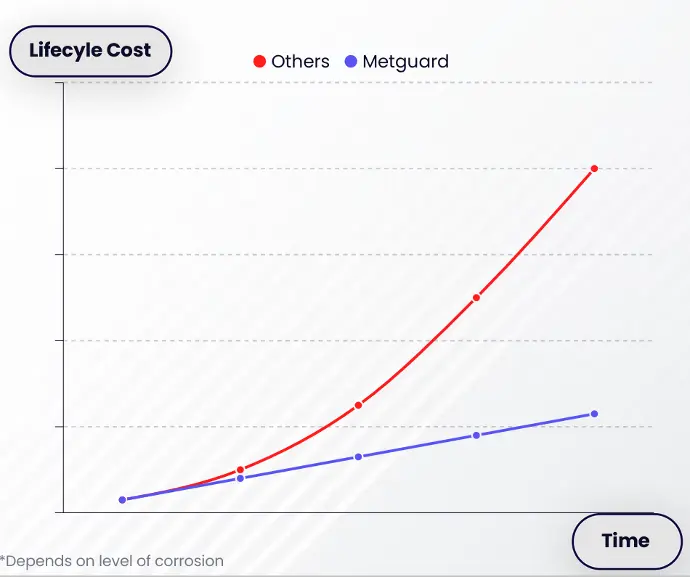
SAVE BY ALMOST 100%
- Lower operational cost as no blast cleaning required.
- Lower maintenance cost as only top coat is to be re-applied. Thus, lesser paint requirement & lower labour cost in future.
- Significant long-term savings in cost as negligible metal scrappage.
- Enhanced workplace safety.
- No disruptions in production.
SIMPLE & EASY APPLICATION
Clean the metal surface
No blasting is required here. Nominal surface preparation, including wire/ brush cleaning will suffice.
Follow mixing instructions
Open the Metguard cans and follow the simple mixing instructions provided.
Apply on metal surface
Apply Metguard coatings directly on the metal surface, even if it is already rusted. Application can be done by brush/spray/roller/ airless/pneumatic gun.
Stop Corrosion
Wait for proper drying and stop the corrosion of metals completely.
COAT IN ANY WAY, IN ANY COLOUR
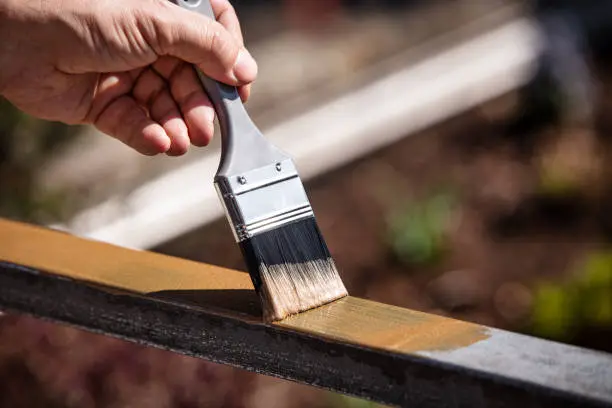
Brush
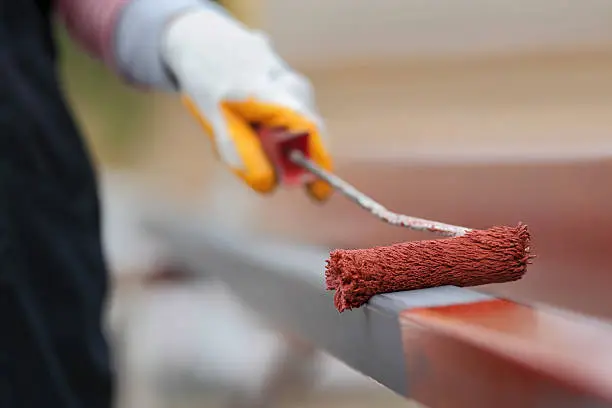
Roller
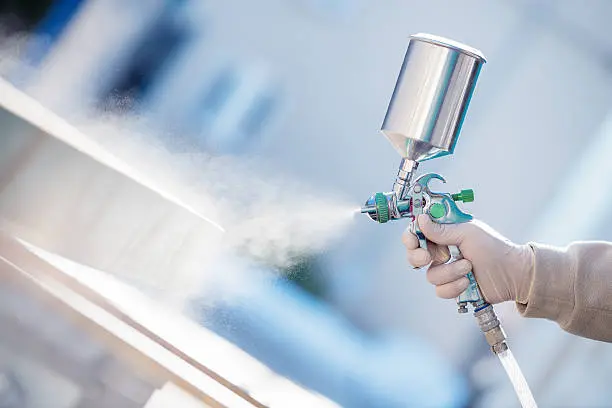
Spray/ Airless Gun
WHY METGUARD?
OTHERS
- Abrasive blasting required
- High maintenance cost
- Very poor performance in harsh environments
- High cost of metal scrappage
- Major disruptions in production
- Involves environmentally hazardous processes
METGUARD
- NO abrasive blasting required
- LOWEST maintenance cost
- UNMATCHED performance in harsh environments
- MINIMUM cost of metal scrappage
- NO disruptions in production
- ELIMINATES environmentally hazardous processes
SAVE METAL, SAVE EARTH
BUILDING A GREENER FUTURE
- Reduces the need for hazardous methods like galvanizing and abrasive blasting.
- Eliminates the use of toxic chemicals and reduces substantial energy consumption.
- Extends the lifespan of metal infrastructure, minimizing waste and reducing the frequency of replacements, thereby reducing carbon footprint.
- Helps preserve natural resources and decrease greenhouse gas emissions.
- Promotes a healthier planet for future generations.
PROUDLY BROUGHT TO YOU BY VISIONCRAFT GROUP
Join us in our mission to create a safer, more resilient, and sustainable future for our planet.