STEEL INDUSTRY
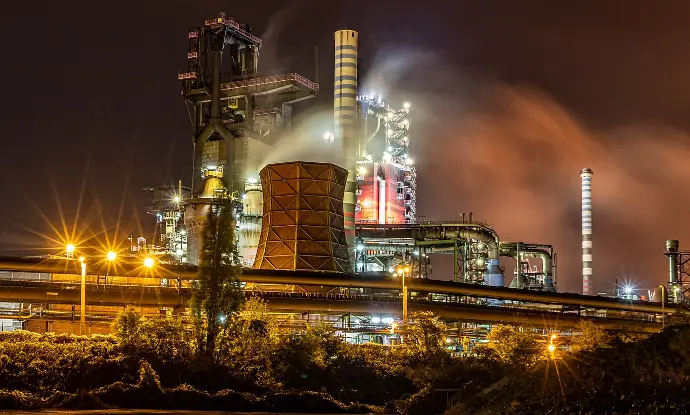
Corrosion in Steel Industry
Steel making involves reduction of iron ore to iron which is the principal ingredient of steel. This is accomplished by carbonaceous inputs derived from coal either in solid or gaseous forms. Apart from being one of the largest emitters of carbon dioxide, steel manufacturing liberates sulphur contained in the ores as well as in the fossil fuel in the form of sulphur and nitrogen oxides together with ammonia, etc. Hydrogen sulphide (H2S) however is the major corrosive pollutant released during steel manufacturing and slag handling processes. While all these oxides form acids in the presence of moisture, sulphur products cause maximum destruction to infrastructure through sulfidic corrosion.As is well known this is one of the worst forms of attack which may cause severe internal stresses in steel infrastructure. Downstream processes like cold rolling employ hydrochloric acid which goes through acid regeneration process to restore its strength. In addition fluxing agents and molten zinc used in galvanizing plants cause high emissions. All such processes emit extremely corrosive acid vapour that affect all steel structures in the vicinity. Further, multiple tank pre-treatment of coated steels prior to coil coating necessitate corrosive liquid discharge and chromate based aqueous streams which are known carcinogens.
THE METGUARD ADVANTAGE
NO ABRASIVE BLASTING NEEDED
Say goodbye to sand/shot/grit blasting—Metguard provides unmatched corrosion protection without any complex surface preparation.
CAN BE APPLIED DIRECTLY ON RUSTED SURFACE
Metguard can be applied directly on rusted surfaces without the need for extensive surface preparation. Only the removal of loose rust will suffice, making it a highly efficient and cost-effective solution for corrosion protection.
NO ELABORATE MAINTENANCE
Easy recoatability requiring minimum surface preparation, only recoating the top coat at specified intervals will suffice. No need to remove existing coating like in other coatings.
No Metal Loss
No loss in thickness of
structural steel as it
prevents underfilm
corrosion, ultimately preventing metal scrappage.
Major Cost Savings
Minimal surface
preparation and longer
metal lifespans lead to
extremely low lifecycle
costs.
Fully-Eco-Friendly
Chromate free, lead
free, halogen free,
isocyanate free, non
toxic, environment
friendly product
Acid/Alkali Resistant
Exemplary
performance in
intensely corrosive
atmosphere, acidic
and alkaline, and
saline.
Heat Resistant
Excellent thermal
resistance -
withstands sustained
corrosive exposure
up to 200°C.
Toughness & High Cohesive Strength
Outstanding
performance in all
weather conditions
and in all types of
corrosive areas.